The behavior of industrial insulation in case of fire
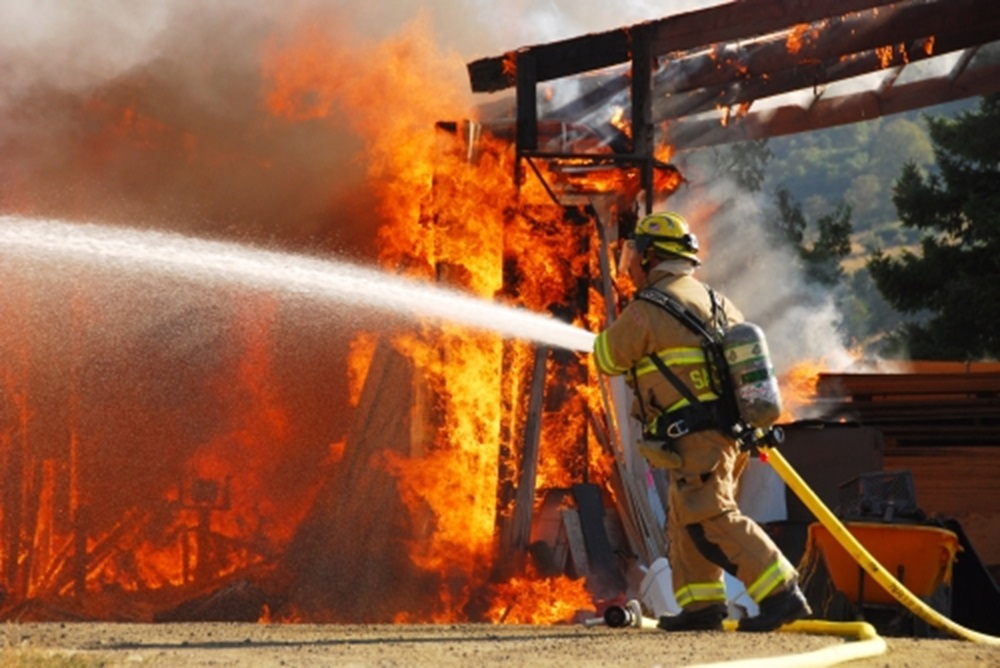
Industrial fires claim multiple lives and millions of dollars in direct and shut-down costs annually. Their prevention should be sought in all aspects of industrial design, including insulation. However, much confusion has surrounded insulation material combustibility and toxicity. Misleading terminology based on some equally misleading testing methods has led to the questionable evaluation of the fire and toxic smoke risk.
THE EFFECT OF FIRES ON HUMAN BEINGS
When people think of fire as a cause of death, they often think of flames; however, in a list of the four ways in which fire can kill, flames are the least likely cause of death.*
Asphyxiation - Fire consumes oxygen from the surrounding atmosphere, thus reducing its concentration. If the oxygen concentration falls below 17%, critical thinking and coordination may become difficult. When concentration falls below 16%, attempts to escape the fire may be irrational, wasting vital seconds. With further drops, a person loses his muscular coordination for skilled movements, and muscular effort leads rapidly to fatigue. Breathing ceases when the oxygen content falls below 6%.
Exposure to super-heated air or gases - With temperatures above 150 °C (300 °F), loss of consciousness or death can occur within several minutes. In addition, hot smoke with high moisture content is a special danger since it destroys tissues deep in the lungs by burning.
Smoke and toxic products - Inhalation of smoke or the products of incomplete combustion, can kill without any exposure to flames. In addition to carrying toxic products, thick smoke may be laden with organic irritants, such as acetic acid and formaldehyde. In the early stages of a fire, the irritants which attack the mucous membranes of the respiratory tract, are often the more significant danger. In addition, smoke also blocks the visibility of exits, making it even more difficult to for attempting to flee the dangers of a fire.
Many toxic components of smoke are responsible for injury or death. These substances include but are not limited to, carbon monoxide, oxides of nitrogen, aldehydes, hydrogen cyanide, sulfur dioxide, and ammonia. Furthermore, there is ample evidence that the hazard of two or more toxic gases is greater than the sum of the hazards of each, and low oxygen levels and high temperatures may increase the toxic effects. In addition to toxic gases that attack the lungs, there are irritants that attack the eyes with blinding effects, preventing escape. Some fire gases dull the senses of the victim or his awareness of injury.
Flames - Since the previously mentioned factors can debilitate, confuse, blind, or kill with little or no warning, thinking that advancing flames will always be sufficient warning for escape may be a fatal gamble.
THE MISCONCEPTION OF THE ROLE AN INSULATION MATERIAL HAS IN FIREPROPAGATION
Thermal insulation is recognized as playing a potentially active role in fire propagation, either by being inherently combustible or by absorbing (wicking) liquids that are themselves combustible. Contributing to this danger is a frequent misunderstanding of tests, classifications, terminology, and the protection provided by specific materials. References to “self-extinguishing” and “fire retarding” are often interpreted as the equivalent of “noncombustible.”
In most cases, it is not flames, but the smoke and toxic fumes resulting from burning (including “slow-burning” or “self-extinguishing” materials) that cause the highest rate of death or injury.* In fact, of the numerous ways by which fire can kill, flames are the least likely cause. The standard “fire triangle” model illustrates the three elements a fire needs to ignite and keep going: a combustible material, an ignition source, and a combustion supporter. Eliminate any one of these components and an ongoing fire is not possible. For this reason, it is advisable to use a completely incombustible material, eliminating one of the three elements which contribute to fire propagation.
A CLOSER LOOK AT FIRE TESTING
Nearly all manufacturers make claims related to the performance of their insulation materials in situations related to fire exposure. Fire testing often gives varying, ambiguous, or even nontransferable data. For example, the ASTM E84 - Standard Test Method for Surface Burning Characteristics of Building Materials and E136 - Standard Test Method for Behavior of Materials in a Vertical Tube Furnace at 750°C, are often viewed as the industry-wide standard for fire testing of insulation materials. However, a review of the test methodology one can conclude that the tests do not appear directly related to the reality of a real industrial fire. The results of these tests can be significantly altered using fire-retardant additives. While additives can reduce flame spread ratings of plastic foams under test conditions, these may have little retardant effect under actual fire situations.
Other conditions that can significantly affect actual-vs-tested fire behavior are the substrates on which insulation is applied, and the rate at which maximum temperatures are attained in chemical or petroleum fires compared with structural or building fires.
COMMON INSULATION MATERIALS AND THEIR BEHAVIOR IN CASE OF FIRE
Fibrous Insulation Materials
Fibrous Insulation is composed of small diameter fibers which finely divide the air space. The fibers may be organic or inorganic and often held together by a binder. Typical inorganic fibers include glass, rock wool, slag wool, and alumina-silica. The most widely used insulations of this type are fiberglass, mineral wool, fibrous microporous, and aerogel-infused materials. They are produced in a variety of forms suitable for specific functions and applications. These include blankets, boards, and pre-formed shapes for the insulation of piping and equipment. Fiberglass, mineral wool, and other inorganic fibrous insulation materials are generally considered to be non-combustible or have limited combustibility. Most mineral fiber insulation products are either Euroclass A1 or A2 (as per EN 13501- Fire classification of construction products and building elements) and will not significantly contribute to a fire. Fibrous microporous aerogel blankets are typically categorized as Euroclass A2 and therefore are considered to have limited combustibility.
When selecting insulation materials for hydrocarbon processing installations, an important design consideration that needs to be taken into account is the risk of absorption of liquid or gaseous hydrocarbons by fibrous insulation materials.
Plastic Foams
Generally, inorganic insulation materials do not contribute to fire or the development of smoke or toxic fumes, but the same cannot be said for organic insulations – especially plastic foams. In fact, polyurethane, polyisocyanurate and phenolic foams can introduce serious fire hazards: rapid flame spread and attainment of extreme temperatures, high levels of dense smoke, and/or generation of toxic or flammable gases or chemicals. Manufacturers’ literature for these products includes numerous warnings and precautions.
Plastic foams often rely on fire retardants that do slow flame spread but, in many cases, they can contribute to the problem with their own toxic fumes. Furthermore, the gas diffusion process which occurs on these foams can create an additional risk under certain circumstances. Rigid polyurethane and polyisocyanurate foam can absorb combustible gases, such as low molecular weight, highly inflammable hydrocarbons. Therefore, if used in applications where such exposure may occur, the foam must be protected by a gas-impermeable membrane.
Calcium Silicate / Perlite
The majority of perlite and calcium silicate insulation materials are classified as non-combustible and sometimes used as passive fire protection for industrial installations. However, the highly absorptive nature of these materials can affect fire safety and increase the fire risk significantly. Porous insulation such as calcium silicate offers a large reaction surface in the face of poor heat dissipation conditions, and this, along with possible catalysts from the insulating material can cause a temperature buildup. This temperature buildup can result in the ignition of the fluid when the saturated insulation is exposed to air.
Perlite often contains organic-based water repellents. These water repellents can be destroyed by temperatures over 200 °C (392 °F) and by petrochemicals. In the case of flammable liquids, absorption can significantly increase fire potential as wicking danger increases as soaked insulation could auto-ignite when interacting with oxygen at a certain temperature.
The FOAMGLAS® Cellular Glass Insulation Solution
Cellular glass insulation has been subjected to scores of national and international tests, including ASTM E-136, ASTM E-84, EN ISO 1182 - Reaction to fire tests for products — Non-combustibility test, EN ISO 1716 - Reaction to fire tests for products — Determination of the gross heat of combustion and BS476 - Fire tests on building materials and structures, to name a few.
In these tests, samples are subjected to furnace conditions, and both sample and furnace temperature changes and flame development are monitored. If any of the strict conditions are exceeded, a material is classified as combustible. FOAMGLAS® cellular glass insulation has undergone rigorous testing and is classified as noncombustible. This means that using cellular glass insulation helps to eliminate a major component of the earlier discussed “fire triangle.”
As discussed earlier, just because a material is classified as non-combustible, it does not mean that fire risk is completely mitigated. The absorptive nature and composition of the material can contribute greatly to fire and smoke development and increase overall fire risk.
FOAMGLAS® insulation has been widely tested and proven by real-life situations to be non-absorptive to combustible liquids or gases. The issues with absorption that non-closed cell materials suffer from are eliminated when using closed-cell FOAMGLAS® insulation.
This is also the reason why engineers often specify non-absorptive, non-combustible cellular glass insulation systems as the recommended system for applications with a risk of leaking organic fluids.
Finally, the inorganic nature of cellular glass insulation helps to minimize the potential fire risk of condensed hydrocarbon gases or liquid oxygen as it has proven to minimize the dangers associated with oxidizing organic materials.
Additionally, this also is the reason why FOAMGLAS® insulation does not produce toxic smoke or gases in case of a fire.
Real-life situations have validated test results that showed a smoke development index of zero. This contributes to the overall fire safety by maintaining fast and safe access to escape routes and allowing people to reach emergency services fast.
Conclusion
Insulation materials play an important role in the fire safety of buildings and installations; however, not all insulation materials react the same in case of fire. Designers should consider a wide range of when specifying insulation systems for fire protection.
Material properties such as absorption, the potential for development of smoke and toxic gases, as well as combustibility should be considered as part of the strategy for total fire safety of an insulation system.
We can conclude that a closed-cell, nonabsorbent, incombustible cellular glass insulation system that does not add to the spread of fire nor produce smoke or toxic gases, can help to ensure maximum fire safety.