Emittance in determination of the jacketing temperature
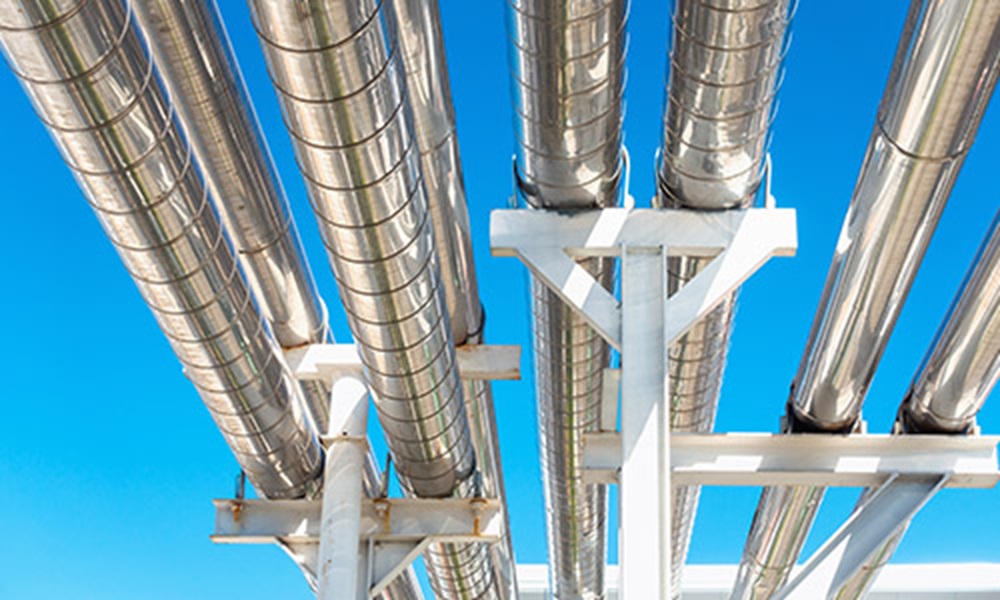
The effect of a change in surface optical characteristics between a high emittance and a low emittance jacketing results in a difference in surface temperature and heat transfer. For pipe operating below ambient temperatures it is important to avoid condensation. Specifying a jacket with a higher emissivity results in a higher surface temperature and consequently a smaller chance of condensation.
A pipe maintained below ambient temperature is provided with an insulation system to reduce the heat gain by the pipe and to reduce and possibly prevent the condensation of atmospheric moisture.
The insulation system should include an insulating material with high thermal resistance to impede the flow of thermal energy through the system and into the pipe. Insulation is usually covered to provide some mechanical protection and to retard the flow of moisture into the system. When selecting a suitable jacketing or coating, one must consider the mechanical, chemical, thermal, cost, and moisture conditions of the installation.
Metal jacketing are manufactured from metal sheets such as aluminum, stainless steel, aluminized steel, galvanized steel, and zinc galvanized steel. Non-metallic jacketing is often made from rigid plastics, laminated foils, fiberglass or flexible membranes. Lastly, there are protective coatings which serve a similar purpose and mostly consist of inorganic or organic mastics that are often used in conjunction with reinforcing fabrics.
JACKETING PROPERTIES
The jacketing is made of materials that are thinner and a much higher conductor of thermal energy than the insulation. Thus, the material of the jacketing contributes very little to the thermal resistance of the system.
Any effect that the jacketing material will have on the heat transfer characteristics of the system will be due to the surface properties and not the bulk properties of the jacketing. The thermal energy gained by the system will be due to radiation and convection processes between the surface of the system and the ambient environment.
It is important to consider this during the design stage since it may have a strong influence on the thickness of insulation required. On below ambient temperature lines, the thickness needed to prevent condensation will be different depending whether an emissivity of 0.9 for a dark reinforced mastic or an emissivity of 0.1 to 0.2 for an aluminum jacketing is in the calculations.
OPTICAL PARAMETERS
The ability of an opaque surface to interact with thermal radiation involves the optical parameters, emittance, reflectance, and absorptance.
The emittance, E, of a surface compares the ability of a surface at a given temperature to emit radiation relative to a surface which emits the maximum energy at the same temperature. Such an emitting surface is called a “black body,” and can be experimentally achieved by means of a cavity with a small exit hole formed in a solid, which is maintained at a uniform temperature.
The radiation emitting characteristics of such a cavity are independent of the material of which the cavity is made and vary in a simple way with temperature. This cavity radiator is thus the ideal solid as far as radiation emitting characteristics are concerned.
When the thermal radiation impinges upon an opaque surface, the energy is either reflected or absorbed, thus: R + A = 1
Where R, the reflectance, is the fraction of the incident radiation that is reflected from the surface and A, the absorptance, is the fraction of the incident radiation that is absorbed by the body.
If an opaque body is placed within an isothermal cavity and allowed to come to thermal equilibrium with radiation the only means of heat transfer between the body and the cavity walls, the emittance and absorptance of the body are equal. If the emittance and absorptance were not equal, there would be a net energy interchange between the body and the cavity wall and the bodies’ temperature would change which would contradict the assumption that the system is in equilibrium. Therefore, E= A and thus R + E = 1.
It should be noted that the values of R, A, and E are all assumed to be valid only for radiation interchange between objects at about the same temperature. Thus, the absorptance for solar radiation for a given material can differ considerably from the emittance of the same material at ambient temperatures.
BEST CASE SCENARIO
Consider a below ambient pipe that is protected with an insulation system. Assume that the jacketing is composed of a material that is a perfect emitter. This assumption implies that the jacketing material absorbs all radiation impinging on it and thus reflects no radiation.
The rate at which the pipe gains energy from the ambient surroundings will be primarily due to the thermal resistance of the insulation and to the magnitude of the temperature difference between the pipe and the surroundings. The jacketing gains energy by radiation from the surroundings and by convection due to the temperature difference between the jacketing and the atmosphere.
The rate of energy flow to the jacketing material depends upon the magnitude of the temperature difference between the jacketing and the surroundings. The jacketing assumes a temperature so that the rate of energy flow to the jacketing surface exactly equals the rate of energy flow in the insulation material.
Now consider the case where the jacketing is composed of a material that is a perfect reflector. The assumption implies that the jacketing material absorbs no radiation impinging upon it and that its emittance is zero. Therefore, convection is the only heat transfer mechanism by which the surface can acquire energy. Due to the absence of radiation the surface temperature will decrease. The temperature difference between the surface and the surroundings increases which allows more energy to be transferred by convection compared to the case with the perfect emitter surface.
However, the total heat transfer is smaller compared to the total heat transfer from radiation and convection with a perfect emitter. This is expected as the difference between the surface temperature and the service temperature is smaller. The thermal resistance of the insulation on the other hand remains the same as the optical characteristics of the jacket surface have no influence on this. Therefore, the heat flow in the insulation material decreases and consequently also the energy flow from the surroundings to the surface of the jacket.
The above discussion can also be applied to a hot pipe protected by an insulation system. In this case, the energy flow is outward through the insulation and jacketing material to the ambient temperature.
Assume that the emittance of the jacketing material is reduced by changing the surface from a perfect emitter to a perfect reflector. The temperature of the surface increases because it loses no heat by radiation. This decreases the difference between the service temperature and the surface temperature. As a result, the heat flow through the insulation material decreases and therefore also the total heat loss to the surroundings.
The heat loss by convection will increase because of the larger difference between the surface temperature and the ambient temperature.
The effect of emittance on surface temperature
The effect of a change in surface optical characteristics between a high emittance/poor reflectance and a low emittance/high reflectance results in a difference in surface temperature and heat transfer.
For a cold pipe it is very important to avoid condensation. A jacket with a higher emissivity results in a higher surface temperature and consequently a smaller chance of condensation. For a hot pipe condensation is unlikely which is why a jacket with a lower emissivity can be chosen to help with reducing the heat loss.
This can be demonstrated with an example of a cold pipe operating at -50 °C (-58 °F) and an ambient temperature of 20 °C (68 °F). A jacketing with an emissivity of 0.1 results in a surface temperature of 10 °C (50 °F) and a heat gain of 35 W/m² (11 BTU/h.ft²). Using a jacketing with an emissivity of 0.9 will lead to an increase of the surface temperature to 15 °C (59 °F) and a heat gain of 38 W/m² (12 BTU/h.ft²).
A hot pipe operating at 150 °C (302 °F) and the same ambient temperature, an emissivity of 0.1 results in a surface temperature of 42 °C (107 °F) and a heat loss 97 W/m² (30 BTU/h.ft²). An emissivity of 0.9 decreases the surface temperature to 32 °C (90 °F) and increases the heat loss to 104 W/m² (33 BTU/h.ft²).