What causes condensation in buildings?
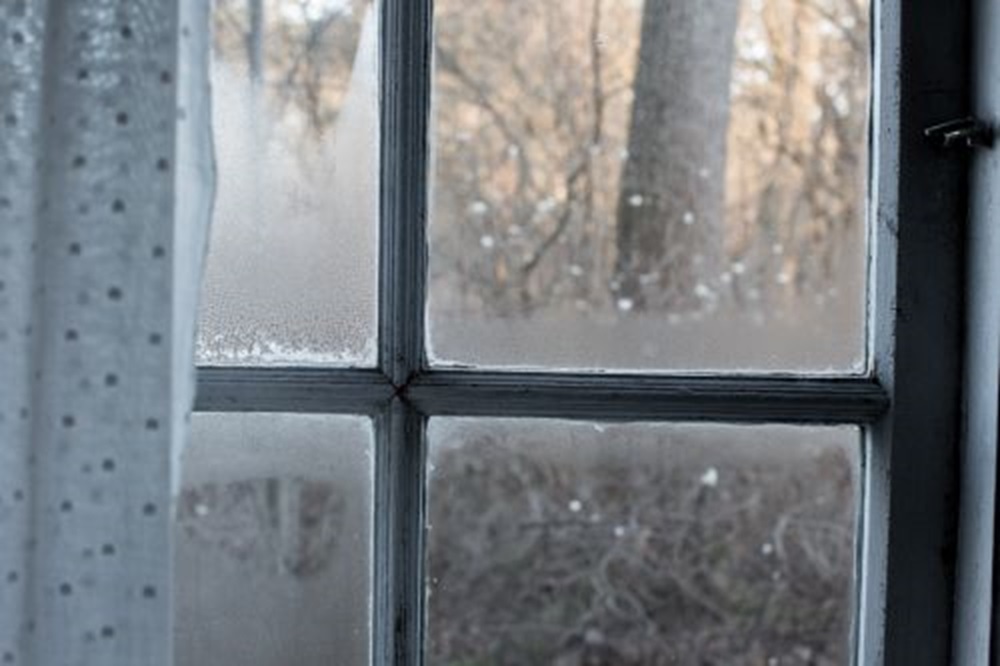
Regardless of the design philosophy or construction method of a building, a failure to understand the principles of condensation risk can result in a range of issues - from problems with internal surface finishes, to much deeper building fabric failures such as the loss of thermal performance, structural corrosion and defects.
Temperature and humidity
Two environmental factors are at the heart of condensation risk: temperature and humidity. Temperature can be expressed as Celsius (°C), or using the SI unit of Kelvin (K).
When we describe internal temperatures, we are talking about the temperature of the air within the structure and how it changes in response to building physics and occupant behaviour. External air temperature is predominantly a function of weather and climate.
Humidity measures the amount of moisture contained within the air, in the form of water vapour (the gaseous phase of water). Absolute humidity is the actual mass of water vapour present in one cubic meter of air, regardless of temperature, and is expressed as g/m3 or kg/m3.
Relative humidity (RH) takes the temperature of the air into account, and is a measure of the amount of water vapour in the air as a percentage of the total amount of water vapour the air can hold at a given temperature.
Temperature curves
Through any thermal element forming part of the building envelope - whether a floor, wall, or roof - the temperature decreases in the direction of the movement of heat energy (usually from inside to outside in northern hemisphere climates).
The rate at which it decreases is dependent on the thermal conductivity and thickness (i.e. the thermal resistance) of the materials that make up the thermal element. Figure 1 shows a temperature curve through a flat roof build-up, based on an internal temperature of 20°C and an external temperature of 0°C.
The temperature at the interface of each material layer can be calculated. A temperature curve is independent of the building envelope’s overall energy efficiency.
Dew point temperatures and condensation risk
The warmer the air temperature, the greater the quantity of water vapour the air can hold. If the air temperature increases, its capacity increases; if the air cools, its capacity decreases. When considering water vapour content, at any particular temperature.
When the air is at maximum capacity, the air is said to be saturated and the RH (relative humidity) is 100%. For a given quantity of water vapour in the air, when 100% RH is reached, this is the dew point temperature. At 100% RH, if the temperature cools or the quantity of water vapour increases, there is more water vapour present than the air has capacity for; the excess water vapour is deposited in liquid form, as condensation, on the coolest surface.
The addition of ventilation and moist air extraction reduce the RH and work alongside the insulation system to reduce or prevent surface condensation within high humidity areas such as swimming pools, kitchens and bathrooms. Surface condensation can be present in many everyday situations.
Some examples:
-
In busy rooms (such as classrooms), people produce a lot of water vapour through respiration and perspiration. Although their body heat will raise the air temperature as well, the quantity of moisture vapour may be too great and condensation is seen on a cold window.
Condensation may also be deposited on poorly insulated areas of walls and roofs with a locally colder surface temperature, especially if the external air temperature drops.
-
Turning on a hot tap or shower increases the moisture content of the air and causes condensation on the cooler surface of a window or mirror.
-
In summer, after taking a cold drinks bottle from the refrigerator, condensation forms because water vapour within the warm air condenses against the cold surface of the bottle.
-
On cold mornings we find occasionally ice on the interior surface of a car windscreen.
-
Warm air within the car cools at night and water vapour within that warm air condensates on the interior side of the windscreen. As temperatures drop further that condensation gradually turns to ice.
When water vapour within the building fabric reaches the dew point temperature, this results in condensation being deposited within the structure. This is referred to as interstitial condensation. If the interstitial condensation does not dry out, and continues over a period of years, the accumulation of water will reduce thermal efficiency, damage building materials, and risk the integrity of structural components and fixings.
Vapour permeability of the building fabric
Where a differential in vapour density exists between one side of a construction and another, vapour pressure is generated, this causes a natural movement of vapour to occur. The movement is relative to the vapour permeability of the materials in the construction.
The dew point is where the air at a particular temperature can hold no more moisture in the form of water vapour (see figure 2), and the vapour returns to a liquid (water).
The dew point can occur at any place within the building fabric. If water vapour passing through the building fabric reaches a location at the dew point temperature, the vapour will condense. It’s the job of the insulation to provide thermal performance and ensure the dew point temperature is not present within the construction.
Assessing condensation risk based on temperature and humidity
The Mollier Diagram (figure 3) shows temperature (X axis) against absolute humidity (Y axis). The curves on the chart plot relative humidity RH at different percentages %, including a saturation curve for 100% RH.
This illustrates the difference in moisture content required for condensation to occur at the inside and outside of a building element.
For example: The diagram shows
- for 50% RH, and an air temperature of 0°C requires a humidity of 1.88 g/kg dry air.
- for 50% RH, and an air temperature of 20°C requires a humidity of 7.26 g/kg dry air.
As another example: The diagram shows 100% RH Saturation
- for 100% RH, and an air temperature of 20°C requires a humidity of 14.70 g/kg dry air.
- for 100% RH, and an air temperature of 0°C requires a humidity of 3.77 g/kg dry air.
Determining dew point temperatures
Calculating the predicted dew point temperature based on relative humidity and vapour permeability of construction materials, and plotting it against the temperature curve, can help to show if there is a risk of condensation occurring within the building fabric. Thermal elements must be designed for building thermal performance (U value) and to avoid the dew point occurring within the structure of the building. Figures 4 and 5 show some examples.
Putting this calculation into practice. The following are examples of how we can use relative humidity and dew points to better understand our buildings and internal climates.
-
For a building with Internal air at 21°C and 50% RH.
-
The humidity level is 7.7 g/kg dry air, which means 100% RH (the dew point) would occur at 10.2°C. Internal air at 15°C and 70% RH.
-
The humidity level is 7.41 g/kg dry air, which means 100% RH (the dew point) would occur at 9.6°C.
-
With a swimming pool environment. The air at 26°C and 65% RH, the humidity level is 14.5 g/kg. This means 100% RH (the dew point) would occur at 19.8°C, showing the potential for condensation in any humid environment (including kitchens and bathrooms)