Gasunie
Rotterdam, the Netherlands
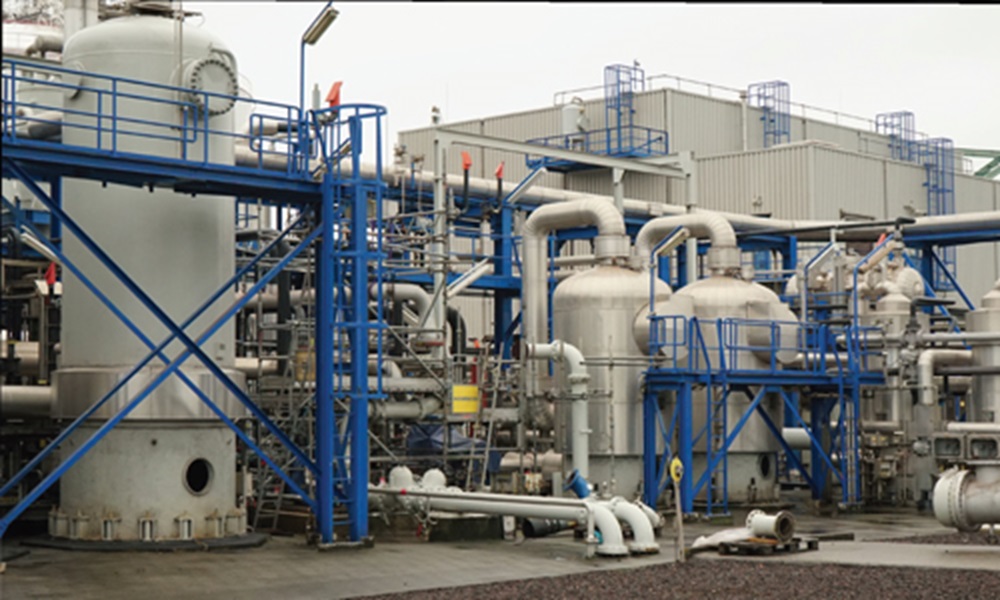
FOAMGLAS® insulation installed on Peak Shaver at Gasunie, The Netherlands.
N.V. Nederlandse Gasunie (short form: Gasunie) is a Dutch natural gas infrastructure and transportation company operating in the Netherlands and Germany. Gasunie Peakshaver BV is the owner of the LNG plant on the Maasvlakte, which can be deployed on days when extra gas for domestic consumers is required due to severe frost.
The peak shaver operates when daily temperatures drop near 0 °C (32 °F) so modifications take place during warmer months to allow for operation during the winter period.
All four Bently Nevada pumps received a full new insulation system to pump LNG and Nitrogen from the storage tanks into the gas transmission network when necessary. Because they don’t run constantly, temperatures could fluctuate from ambient to as low as -200 °C (-328 °F), which is more demanding for all components than an installation with a continuous temperature. All pumps were over a meter in diameter and close to 4 meters in height, all connected to dozens of meters long pressure pipes.
Gasunie has its own specifications for insulation systems that are based on the CINI norms and other worldwide used regulations. One of the requirements that is specified is the use of an inorganic insulation material for any application with liquid nitrogen, LNG and oxygen. The specification states that, for the insulation of pressure pumps, a FOAMGLAS® ONE™ insulation system should be used based on its properties with regards to safety and use in cryogenic applications.
The first of three layers was dry-applied onto the system, without use of any adhesive or sealants. All FOAMGLAS® ONE™ insulation pieces were factory-coated with a high temperature anti-abrasive coating. This anti-abrasive coating helps protect the surface cells against abrasion due to possible vibrations, and serves as extra protection in systems with cyclic temperatures.
The outer layer of the installed FOAMGLAS® ONE™ system was finished with theTerostat system. This means that all pieces were factory-coated with Terostat PC® FRi, a silicone based product that is also used as an adhesive and to seal joints. The end-result is a system where coating and sealant become one monolithically and hermetically closed solid.
A PE foam foil with anti-perforation layer was installed over the Terostat finish and the stainless steel 304 sheets were installed directly on top. Support blocks, spindles, valves and pressure gauges were also insulated with FOAMGLAS® ONE™ insulation.